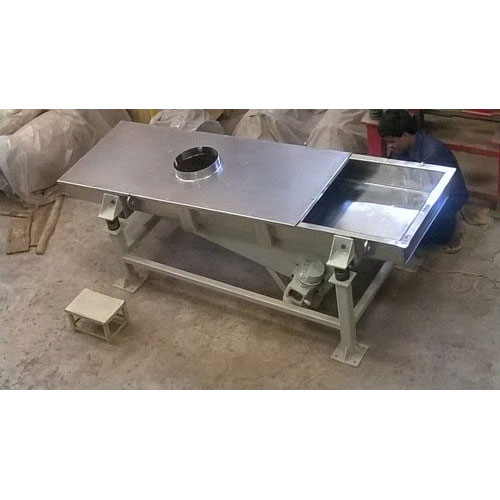
Ask for Price
ORTON
make vibratory conveyors find wide application in cement plants, steel
plants, fertilizer industries, pharmaceutical industries, glass industry
etc, where controlled feeding of material is required. These conveyors
have proved their reliability in transporting bulk material over limited
distances.
Depending on requirement and applications vibrating conveyors are
available in electromagnetic and electromechanical types.
Electromagnetic vibratory conveyors make use of an electromagnetic drive
for generation of vibrations whereas electromechanical vibratory
conveyors are powered by two unbalance motors rotating in opposite
directions. Electromagnetic vibrators are used in applications where
stepless variation of feed rate from 0-100% is required. On the other
hand electromechanical vibrators are used where the feed rate is not
required to be changed frequently during operation or where a relatively
constant feed rate is required.
Electromechanical vibratory conveyors are powered by
two unbalance motors which rotate in opposite directions. These types of
feeders can be supplied in two types viz. trough type and tubular type
depending on the type of application and material being conveyed.
Trough type conveyors
These types of electromechanical vibratory conveyors are suitable where
the material conveyed is granular in nature comprising of medium / large
size lumps and where fine powder content / dust is minimum. However, if
required, the trough can be provided with a co-oscillating cover in
order to prevent dust generated due to vibrations from escaping into the
surrounding environment. In cases where the material conveyed is
extremely abrasive in nature, the trough.is provided with abrasive
resistant liners. These liners are fixed to the main trough by means of
countersunk bolts.
Tubular Conveyors
These types of electromechanical vibratory conveyors are strongly
recommended where the material conveyed has a high proportion of fines
with a tendency to form dust during vibrations. A detachable lid is
provided at both the ends of the tube to facilitate cleaning as and when
required. Inlet and outlet nozzles with suitable flanges are provided.
The inlet and outlet nozzles can be easily connected to the client's
preceeding and succeeding equipment by means of flexible bellows, which
also seals these points.
Advantages
- Very low maintenance required as the motors are extremely robust
in construction and reliable in operation.
- Large magnitude of force can be achieved.
- Amplitude of vibrations can be varied by changing the position of
the centrifugal weights in standstill condition of the motor.
- Extremely simple to connect and operate.
- Depending on the application, motors with different RPM's can be
selected.
Electromagnetic Vibrating Feeders are equipped with
electromagnetic drives which generate vibrations required for conveying
of material. The electromagnetic drives are robust in construction with
very high reliability factor. These conveyors come with a specially
designed controller required for operation of the electromagnetic
conveyor. These controllers convert the input AC supply voltage into
pulsating DC output which results in generation of vibrations. A
thyristor such as a silicon controlled rectifier is used for this
purpose. The firing angle of the SCR can be varied steplessly using a
potentiometer or an analogous electrical signal / PLC signal from an
external command variable unit, which in turn increases / decreases the
amplitude of vibrations thereby controlling the output of the conveyor
as required.
As in the case of electromechanical feeders depending on the material
conveyed, the conveyors can be supplied in two types viz. trough type
and tubular type. Suitable liners in case of trough conveyors are
provided where severely abrasive materials are handled as in the case of
Electro Mechanical Conveyors.
Advantages :
- Easy and stepless variation of delivery of material either
manually or automatically possible.
- Delivery remains generally constant inspite of fluctuations in
supply voltage (± 10% for voltage variation & ± 3% for
frequency variation.)
- Drive is extremely robust and simple in construction.
- Electromagnetic drive is dustproof and is impervious to moisture.
Isolation Of Vibrations
It is of prime importance to isolate the generated vibrations from the
surroundings such as the mounting structures of the Vibrating units.
This is achieved mounting the conveyor on specially designed helical
springs. The spring design varies for electromechanical and
electromagnetic drives. The type of spring used also depends on the rpm
of the motor chosen. Depending on the requirement, the conveyors can be
supplied in base mounting arrangement or suspension mounting
arrangement.
Installation Of Conveyors Under A Bin
Designing of hopper / bins under which the conveyor is installed is
very important in achieving the required capacity. The hopper should be
designed in such a way that the conveyor tray should be relived of the
material column load as far as possible. The bin outlet should be in
such a way that the ratio between the depth of the bin outlet (A) and
the passage height (B) should be between 0.9 to 1.25. This will
facilitate easy flow of the material and help in achieving the required
capacity. A typical installation is shown in the figure below.
A - DEPTH OF BIN OUTLET.
B - PASSAGE HEIGHT.
C - GAP BETWEEN BIN & FEEDER WALL.
D - HEIGHT OF TROUGH.
ORTON make Vibrating screens for grading, extracting and separation
applications.
General
ORTON vibrating screens work on the principle of linear displacement of
materials due to unbalance forces generated by two unbalance motors
rotating in opposite direction. These screens are basically used to
separate coarse materials from fine materials which exist in mixed form.
Depending on the grading size details, the number of decks required are
decided. Generally the screens are provided with one deck or two decks.
In case more than two decks are required for a particular application
then, two vibrating screens can be used in tandem in such a way that the
finest output of the first screen can be fed as the input to the second
screen. The second screen will further grade and separate the material
as required.
The selection ..of the screen deck mesh will depend on factors such as
the material to be screened, whether the material is dry and free
flowing or is moist and sticky, particle size of the material to be
screened, shape of the material etc. Utmost care is to be taken to
ensure that the screen decks do not get clogged as this will result in
reduced screening area thereby affecting the output of the screen.
The screen body is extremely sturdy and rugged made
up of mild steel of adequate thickness. The thickness of the steel
plates depends upon the size of the screen and the selected motor.
Depending on the material to be screened, the sieve analysis and other
related factors, suitable screen decks are provided. Normally these
decks are in the form of wire mesh or perforated plates.
The screens are mounted on the structural framework via specially
designed mounting springs. The selection of these springs will depend on
the total weight of the equipment and the motor rpm. These screens are
usually base mounted, however they can also be suspended if the
situation demands.
The screens are provided with suitable inlet and outlet openings as
required by the customer. The positioning of the outlets will depend
upon the requirement of the customer.
Few typical applications of screens are shown below
Type |
Application |
Screens in cascade |
Separation of mixture of coarse, medium and fine to very fine
particles of material (e.g. Sand) |
Screens for material grading |
Grading of oversize and undersize material (eg. Minerals, Coal,
Gravel) |
Screens for Extracting |
Extracting of very coarse materials from fine material (eg.
Scraping, Coal, Ballast) |
Shakeouts Screens |
Segreating sand from casting |
The above illustrations are indicative only
Standard supply voltage required for the motor is
415 V, 3 Ph, 50 Hz. The motors can be started through a DOL starter
circuit. The panel can be supplied if required by the client.
In order to avoid resonant elliptical oscillations (amplitude of which
are extremely high during stopping), A D.C. braking circuit can be
incorporated which will neutralize the inertial effect of the motors,
thereby stopping the motors instantaneously. This is .an optional
feature and is generally recommended for bigger size motors used in
conveyers and screens.